Revolutionize your paper manufacturing with AI-driven optimization. Enhance efficiency, cut costs, and achieve autonomous operations like industry leaders Arjowiggins and Oji Paper. Embrace the future of smarter production!
Learn more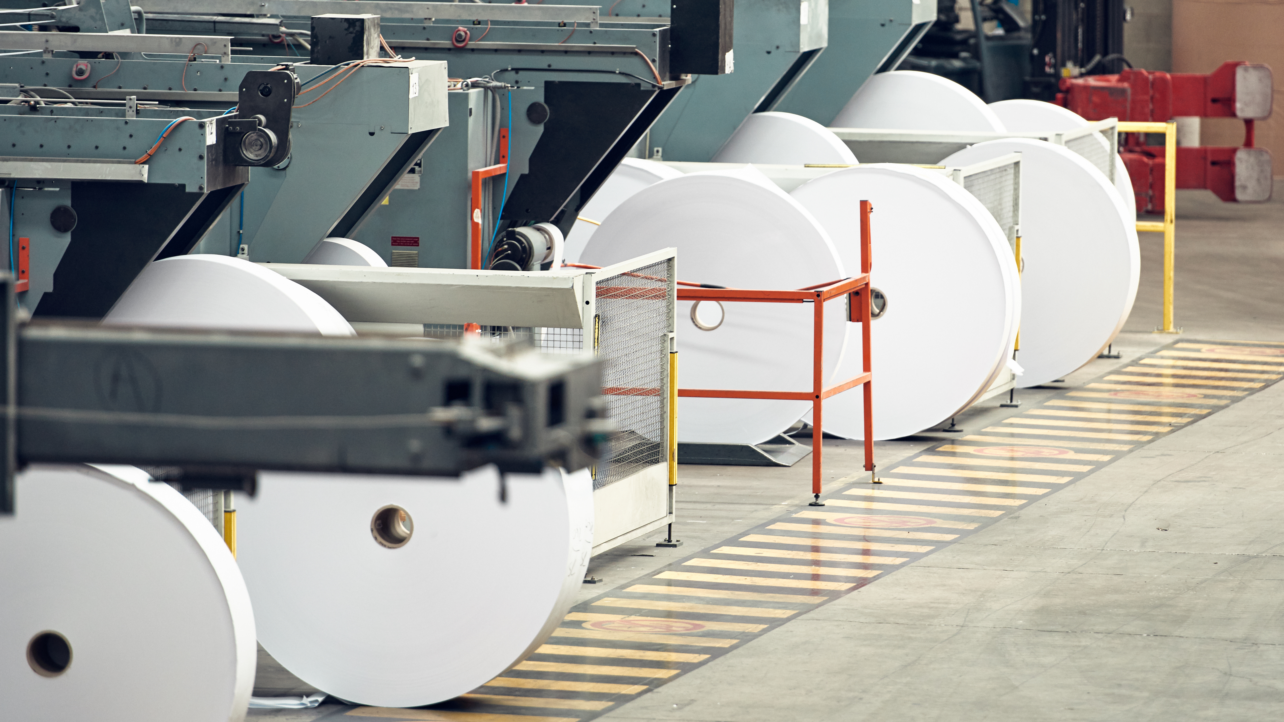
A CPG company struggled with frequent unplanned downtimes causing increased production costs. With Braincube, they reduced downtime and increased OEE.
Minimizing unplanned downtime through automated condition monitoring can greatly reduce manufacturing production costs. Choosing the right condition-monitoring software is a proactive step that enables you to monitor the performance of your machines and assets remotely. Braincube’s IIoT Platform gives you access to real-time condition data that your team can use to react and troubleshoot faster to improve efficiency and scale production. This article discusses different condition-monitoring strategies and solutions that can enhance your organization’s manufacturing performance.
Condition monitoring collects historical and real-time production data to bring situational awareness to industrial teams. Data is processed from PLC inputs, sensors, quality data, vibrations, etc. This increased visibility helps to build machine health and safety predictions, that can be leveraged to reduce cost and risk.
A basic example includes tracking vibrations to trigger alerts to indicate a looming failure or monitoring temperature changes to indicate a safety concern. These types of condition monitoring strategies lend themselves to better performance but also to a preventative maintenance schedule.
In addition to real-time improvements, bringing condition monitoring software can automate your collection of key metrics such as OEE, production conditions and rates, and events. Because this data is usually stored in an industrial network, teams have remote monitoring capabilities to view critical factory floor data from anywhere in the world. Teams can view current and historical performance to make data-driven decisions and even send recommendations directly to the equipment or person needed to make the change.
Condition monitoring solutions are a common tool that manufacturers rely on as it can be highly effective across multiple sites and is usually low risk with high rewards. With IIoT connecting equipment data and enabling bi-directional data flows to different systems, teams can make informed business decisions that improve operations, profit, and safety. These connected machines offer comparable data and analytics of the production process to address current and possible upcoming problems.
Continuously monitoring the condition of equipment and machinery allows for an in-depth understanding of the mechanical operations of your manufacturing process. This helps your team to improve availability, schedule maintenance, and increase yield. Yet, to know how to operate in the best way, you need to first understand how you currently operate, at what frequency, and begin to stabilize your process: condition monitoring is an important stepping stone to consider or expand your digital transformation progress.
When considering a condition monitoring solution, there are several elements to contemplate when investing in insightful analytics. Condition monitoring solutions should combine purposeful tools and tasks to identify and solve problems in the manufacturing processes to ultimately improve operations.
It’s not just about accessing the data, but thinking about your change management approach, and strategic initiatives and making your teams more agile with data. Data is really just numbers until you have the technology (and process!) that can transform it into usable information.
When evaluating if you need new technology or to add functionality to your current stack, be sure to consider the data you may already be collecting. Do you have current smart assets, data sources, or other information that, if digitized, could improve your bottom line? Some type of digital maturity audit should be factored into your decision when implementing condition monitoring. For example, what percentage of your equipment is connected vs legacy equipment? Can you rely on sensor data, or do you need to reimagine your entire line? Identifying which part of your line to monitor can help you find early wins to keep your morale moving through the plant.
For example, apps from Braincube, such as the Machine Status App, allow you to see individual machine performance, including the categorization of unplanned vs. planned downtime. This is an easy-to-implement, low-cost condition monitoring tool that can be leveraged within your current tech stack.
Condition monitoring solutions are sometimes mistaken for something highly complex, expensive, and with a long ramp time. However, with advanced business-ready solutions, manufacturers can leverage a few connectors, data configuration, and an IIoT platform, and you can be up and running in hours. Regardless of edge, cloud, or hybrid architecture, plug-and-play solutions can help you drastically improve performance without a ton of resources.
Braincube’s IIoT Platform takes the data you’re already running on your machines and centralizes it into a platform full of plug-and-play apps. It’s a good consideration for those who are already collecting data, but may not be able to instantly use it in real-time.
We also can help build an architecture for plants with low maturity. At the heart of Braincube is the ability to take incomprehensible data (sensors, PLCs, etc.) and transform it into business intelligence. The benefit of an IIoT platform over niche condition monitoring tools is that it can actually integrate your systems. Now, data is centralized from all of your relevant systems and available to all users. Plus, you don’t need different logins for different software or remember tedious click paths to get to each report you need.
For example, the Braincube Studio App lets teams build custom dashboards to monitor and display the most important information. Because it can also display third-party software, you don’t have to worry about siloed data; it’s all united in a launchpad of information via the Studio App.
An engineer from one of our paper customers said, “The alerts help me to perform maintenance only when needed and before operators discover the problem. Moreover, I can see every machine of my company without leaving my office.”
The ability to have technology that provides insights about the conditions of your equipment no matter where you are allows you to share valuable information with your team. These insights are available to all users, whether near the manufacturing machines or in corporate headquarters across the country.
With complex processes, keeping track of moving data can be highly automated with condition monitoring tools.
Effective condition monitoring outcomes are more likely when you have the right data. This means that you need an increase in both data quality and quantity. Without an effective data source to generate this information and a system to view it in, you’re left to the inefficiency of habits. While there are benefits to word of mouth, intuition, and SME knowledge, driving a culture of data-driven decisions is surprisingly well-accepted by frontline workers who are often bullish about technology.
However, before you dive into the expected results, you need to understand what you want to achieve from condition monitoring. Whether you rely on Value Stream Mapping, metrics like OEE, or other corporate initiatives, knowing why you’re implementing a condition monitoring software will help you to create an effective executive plan.
For example, say you want to optimize energy-intensive assets such as your boilers. You’ll want to rely on tools that help you understand the current machine state and the optimal state.
Condition checking involves examining specifications while the machine is running, reducing the chances of disruptions. This information measures the machine’s condition at a given time using sensors on the machines.
Industrial manufacturing machines collect, extract, store, and display various data points for optimal health and performance. Many machines collect and monitor data from sensors and machine monitoring software to continuously view and analyze this valuable data, turning it into real-time insights and analytics.
Robust IIoT solutions can communicate findings in a comprehensive form and notify them of equipment failures. However, monitoring is only half the battle; having accurate reporting and alerting is critical to efficient condition monitoring. Receiving real-time reports and alerts from Braincube’s Edge Analytics Platform will give your teams real-time snapshots of what is happening around the clock, instead of spending hours trying to make sense of the hundred data points your assets are delivering.
That’s why tools like Braincube’s OEE App, provide substantial time and cost savings. The OEE provides automated real-time OEE calculations, helping you to drastically increase your efficiency. The app provides insights on why you are underperforming in real-time, making it easy to adjust your shop floor strategies and improve over time.
Further understanding the real-time performance and compliance is simpler with Braincube’s Live App. This tool allows you to display comprehensive visuals to enable your team to monitor the condition of your machine sensor intervals continuously. With this app, your team can accurately see what is happening on the plant floor in real-time and improve overall quality and performance with (optional) AI recommendations.
Decathlon, a producer of high-quality, sustainable, and cost-effective retail athletic products, wanted to improve the monitoring of the plant’s production and its day-to-day performance. Decathlon wants a solution that is minimally intrusive to its existing equipment and has a clear view of its overall effectiveness and quality. “Our ambition was to be able to devote ourselves to analyzing data and making decisions, and not simply collecting it,” said Vincent Poquet, director of the Jetlane Decathlon site.
They leverage Braincube’s Edge Apps to track, monitor, and improve their OEE using their new data collection methodology to see things like the default rate for every machine in a single dashboard. By sharing data with the right people at the right time, Decathlon can adapt to any situation.
Braincube’s Condition Monitoring package gives access to real-time place conditions that your team can react to and troubleshoot faster to improve efficiency and scale production. The Counter App tracks the number of products made by each machine. It can be used with data from Machine Status to monitor and improve OEE and other important factory data from anywhere in the world.
“Our ambition was to be able to devote ourselves to analyzing data and making decisions, and not simply collecting it,”
Vincent Poquet, director of the Jetlane Decathlon site.
Condition monitoring is becoming more common across the industry to ensure the safety of the machines and improve efficiency. Many condition monitoring systems are limited in their scope to centralize multiple data sources into a single platform.
An IIoT can integrate monitoring software into a single real-time data portal that teams can access from anywhere and with any device. When creating an IIoT-connected condition monitoring system, many things should be considered, such as your equipment, the data variables you want, and how you plan to use it.
Braincube’s Condition Monitoring App Package makes it easy to track asset performance, OEE, manufacturing production condition, and other important information from the factory floor. This package lets your teams send recommendations remotely and seamlessly produce visibility that empowers success. It helps to further connect processes, people, and results across your entire organization.
Braincube’s condition monitoring applications help you track asset performance, OEE, production conditions, compliance, and other critical factory floor data—from anywhere in the world.
Advanced product traceability helps teams obtain Golden Batch consistently, pinpoint areas for improvement, and keep things running smoothly. Here are six challenges that you can overcome with traceability.
Our digital maturity assessment helps gauge your level of connectivity and aptitude for digital transformation. Gain actionable insights to help you move forward—no matter where you are on your transformation journey.