Revolutionize your paper manufacturing with AI-driven optimization. Enhance efficiency, cut costs, and achieve autonomous operations like industry leaders Arjowiggins and Oji Paper. Embrace the future of smarter production!
Learn more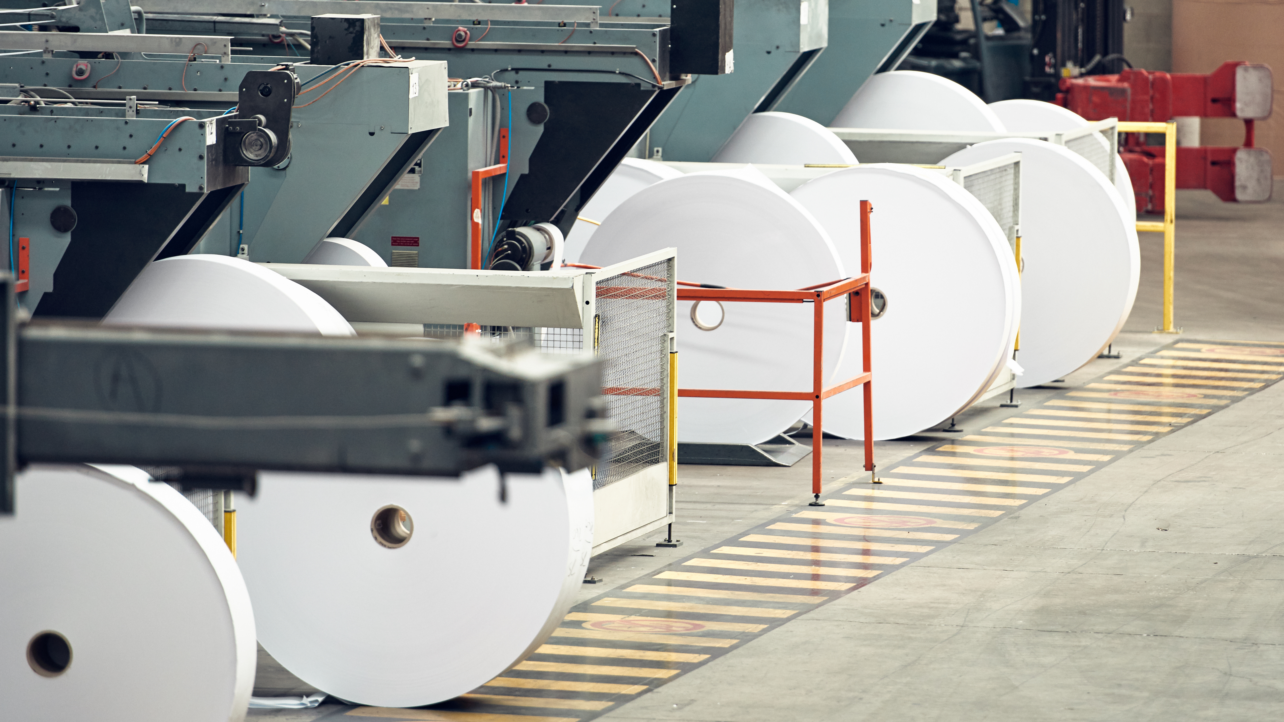
Manufacturing maintenance teams aim to prevent downtime. While this seems like a straightforward directive, preventing downtime is quite complicated given the size and breadth of the machines, systems, and processes involved.
This is why a comprehensive maintenance strategy is crucial for today’s manufacturers.
Maintenance strategies are not always viewed as an advanced business function requiring significant consideration, development, and investment. This is at odds with the importance of preventing downtime. Your maintenance strategy determines how your assets and production capabilities will be cared for going forward. It’s your insurance against costly unplanned downtime events.
This gives rise to the question:
What type of maintenance strategy and technology is most effective in today’s manufacturing landscape: preventative or predictive?
As manufacturing continues to adopt Industry 4.0 technologies and capabilities (hello, Artificial Intelligence and Machine Learning), answering this question has a significant impact. Both preventative and predictive maintenance strategies involve scheduled maintenance and both impact production time. The challenge is determining which strategy best supports the overarching “prevent downtime” mission.
We know many manufacturers are struggling with this decision. To help get a clearer picture of how these maintenance approaches work in the manufacturing landscape, we’ve broken them down and provided some pros and cons. Take a look.
Historically, preventative maintenance has been the go-to strategy for manufacturers. Preventative maintenance requires teams to perform maintenance based on a predetermined schedule/cadence, regardless of whether there are any indications of an issue. Using this strategy, the goal is to have teams perform maintenance work before anything can go wrong.
We liken this approach to getting your car’s oil changed. You get your car’s oil changed every 5,000 miles even though the car is running fine and nothing seems wrong. It’s simply time to get it done.
Preventative maintenance is a sound maintenance strategy. It allows downtime to be planned and scheduled. This isn’t to say there isn’t some technique or strategy behind setting these schedules. For example, usage-based maintenance means that you’re using historical data and known best practices for sticking to a predetermined routine. You’re trying to operate a well-oiled machine—sometimes literally—for as long as you can.
This maintenance is not avoiding machine breaks, because some pieces will follow the expected usage, repair, breakdown, etc. Preventative maintenance is finding a balance between completing too much maintenance, too much downtime, or having too many breaks. Sometimes, you make the best decision for production because there is no good decision in that balance.
Preventative maintenance is also predictable and relatively cheap to implement. It makes it possible for teams to prevent issues and monitor machine health. Like getting your car’s oil changed regularly, it does the job.
However, in today’s fast-paced environment, preventative maintenance presents some efficiency hurdles that can have serious implications. For instance:
The biggest drawback to this maintenance methodology is that it’s based on habits. A plant manager or other management lead determines the timing, the machines, and the work to be performed. It’s difficult to know what information to use when setting different maintenance schedules. Should teams use historical data? Past records? The calendar? The equipment’s manual?
As with car maintenance, preventative maintenance is effective in terms of making sure that machines are, more or less, kept in working order the majority of the time. However, the analog nature of preventative maintenance should be considered when evaluating your maintenance strategy. Will this strategy allow your business to keep pace with the rate of business? Is it the best use of your maintenance teams’ skills, time, and resources?
Predictive maintenance aligns with the Industry 4.0 landscape. Predictive maintenance technology uses data to inform when teams perform maintenance, moving this work to an as-needed basis. It relies on big data analysis to determine the key indicators for maintenance instead of relying on an arbitrary schedule.
For this reason, a data-driven predictive maintenance strategy has enormous benefits:
Predictive maintenance is akin to taking your car to the shop because you get an alert that you’re approaching the ideal mileage for your current tire treads. You are optimizing your repair schedule around usage, data, and schedule.
You have data (in this analogy, maybe an email alert from your service company) that indicates your tires need maintenance. You know you need to rotate or replace your tires soon, but you can schedule a time that works best for you. The data gives you a warning, you address it, and voila you continue on your way.
Teams can perform maintenance before there’s a serious breakdown but without performing unnecessary preventative maintenance.
One reason that many manufacturers still lack a predictive maintenance strategy is that these initiatives rely on advanced data analytics. Teams need to be able to collect and make sense of the machine ecosystem in order to identify as-needed maintenance.
IIoT platforms are designed to facilitate this process. IIoT systems collate siloed data from a variety of systems, equipment, and other “smart” devices. The resulting information can then be used to optimize business results and inform predictive maintenance strategies.
For example, Braincube’s IIoT platform helps teams build a better predictive maintenance strategy via advanced self-service technology, including:
Given the pace that which manufacturing is becoming data-driven, adopting robust predictive maintenance technology ensures maintenance teams are staying in step. It also gives these teams space to bring their own data-driven insights, innovations, and creativity to this critical business activity.
Both preventative and predictive maintenance methodologies are relevant in today’s manufacturing environment. However, more plants are undergoing digital transformation. Advanced computing technologies (e.g. AI and automated condition monitoring) are playing a larger role.
Aligning your maintenance team’s capabilities to these Industry 4.0 technologies helps them achieve their prevent-downtime mission more effectively and efficiently. This means improving their access to advanced self-service analytics and condition monitoring tools.
Preventing downtime is an enormous responsibility. Empower your maintenance teams with a strategy that promotes success.
Learn why predictive maintenance is a better way of working and the technology that can bring this capability to your plants.