Revolutionize your paper manufacturing with AI-driven optimization. Enhance efficiency, cut costs, and achieve autonomous operations like industry leaders Arjowiggins and Oji Paper. Embrace the future of smarter production!
Learn more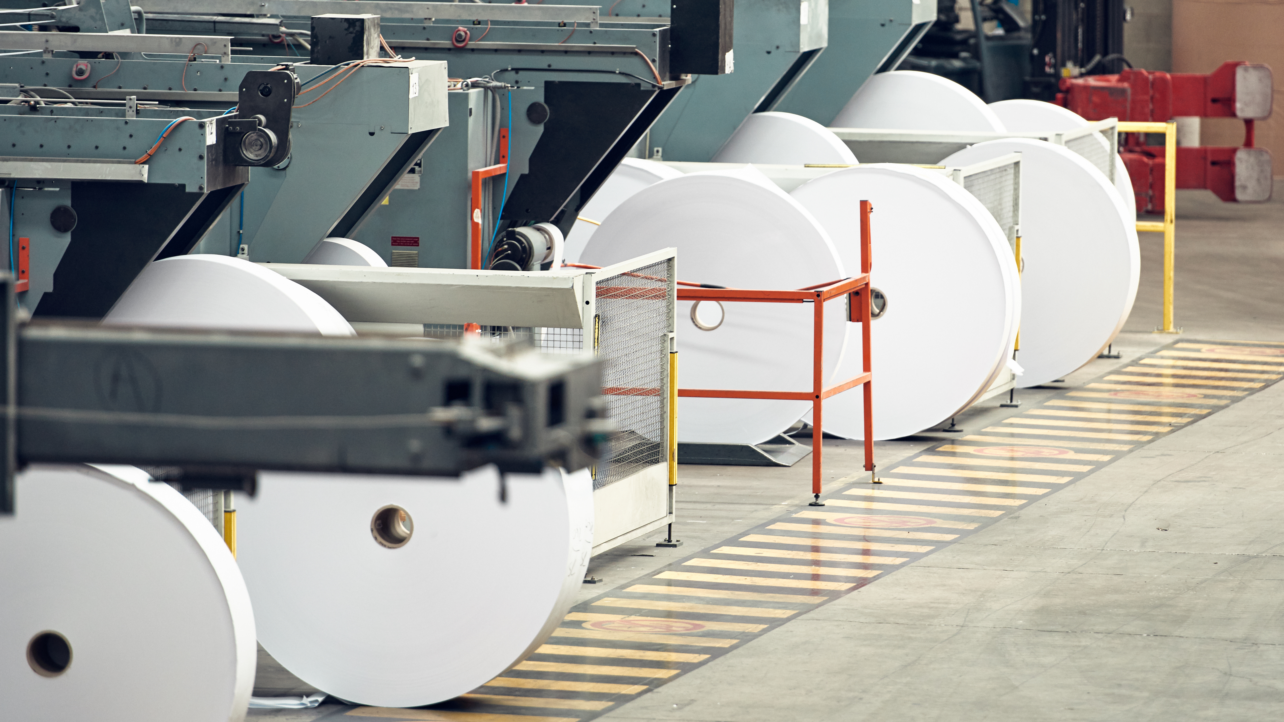
For beverage manufacturers, quality control is always top of mind. Beverage quality control is essential to producing beverages that satisfy customers time and time again. Whether you’re producing beer, carbonated beverages, or specialty spirits, quality plays a leading role in your KPIs and continuous improvement efforts.
However, quality can also be a fickle thing to maintain and perfect. Even if you’re collecting data, issues may still arise that you’re not sure how to fix. The same products produced at different facilities have different taste or color attributes but the processes are the same.
Luckily, today’s Industrial Internet of Things (IIoT) tools can help beverage manufacturers address these concerns. This article explores how IIoT tools—including Edge technologies, Digital Twins, and Computer Vision—can help beverage manufacturers manage and improve their quality control.
When it comes to collecting data, many beverage manufacturers are well ahead of the game. However, collecting data doesn’t mean teams are truly using data. In order to effectively use data, employees need access to clean, reliable data—and technologies to use them in.
Taste and quality can be difficult things to get right for beer manufacturers with multiple facilities. For example, the water source you use in one location may taste different than the water source at another location, which can cause inconsistencies in taste. If you’re a national brand, this can cause some consumers to be frustrated if the product tastes differently depending on where they consume your product.
Tracking each batch’s data and specific measurements in isolated systems (e.g MES, PLCs, Edge, or historian) is tedious and cumbersome. Even with data visualization tools, Smart MES systems, countless sensors, and probably more data than you know what to do with, companies struggle to extract meaningful value from their data.
With product Digital Twins, teams don’t have to fumble through multiple data systems to gather information around each batch. Instead, they can focus on projects that will drive your business forward. A Digital Twin is a digital replica of any process, system, or physical asset. Using a Digital Twin enables you to merge the physical and digital worlds.
Braincube-powered Digital Twins can be built for assets, specific production lines, your end products, or for any other “real world” scenario within a production process. Simply put, Digital Twins automate data compiling and cleaning tasks and make data instantly accessible to technical and non-technical teams to improve process health.
Many beer producers already use an MES to manage quality control. While an MES has immense benefits, a Digital Twin includes data from outside production itself—for example, the weather, supplier raw ingredient information, and even enterprise or financial data. Not only can Digital Twins save teams time when collecting and cleaning data from multiple sources for a study, but Digital Twins make it possible to include production data that don’t exist within your MES.
This means Digital Twins can help teams understand, for example, how variations in source materials (such as water) impact the final product’s attributes. Digital Twins enable teams to get a comprehensive look at your entire manufacturing process. In turn, they can use this information to make valuable optimizations in third-party analysis tools or Braincube’s powerful, user-friendly suite of advanced Business Intelligence applications.
Carbonated beverage manufacturers produce high volumes usually with low margins. It’s difficult to strike the right balance between optimizing production and minimizing costs.
Accurate fill levels play a significant role in keeping costs low and predictable. Even the smallest amount of fill level variability can result in significant financial losses. On the one hand, overfilling means you’re wasting product. On the other hand, underfilling could mean scrapping finished products or spending time and money to delicately refill bottles to the proper amount.
Advanced IIoT technologies can help ensure that fill levels are right where they need to be, time and time again. For example, Computer Vision (CV) is a type of Machine Vision System (MVS) that has been used to improve food and beverage quality control for quite some time. Many manufacturers are likely familiar with the fundamental uses of CV, including detecting product uniformity (e.g., size and shape), but it can also be used to ensure proper fill amounts for beverage manufacturers.
Utilizing autonomous technologies like Computer Vision for the filling process brings immense benefits to carbonated beverage producers. Detecting minute changes in filling volumes may not be possible for the human eye to detect until too much product has moved through the line. CV ensures that discrepancies are detected early, saving the company money while helping employees stay on track with quotas.
Identifying a problem with CV is just the first step. Given the huge volumes and rapid speed of carbonated beverage production, declining performance must be caught quickly in order to minimize the repercussions.
Tools like Braincube’s Alerts application can ensure that the right teams are notified quickly when something starts to go astray. This application can be set to notify specific teams when specific events occur. The Alerts app can help teams minimize waste, prevent unnecessary downtime, and reduce safety hazards by reacting right away—before other areas of production are impacted.
Using the fill level example, let’s say that a CV identifies that bottles leaving the filling machine are filled above the set threshold. This anomaly triggers the Alerts app to notify the shop-floor team. In turn, they can start investigating why the machine is overfilling, resulting in both a rapid reaction time and less wasted product.
Spirits have lengthy processes that can last hours or days, even before being barrelled and stored for years. It can be difficult to track a single batch over multiple, time-consuming steps like fermentation and distillation.
Braincube-powered Digital Twins are unique in that they also account for time lags between different steps of your processes. This is especially valuable for spirits producers.
Digital Twins make it easier to track end-to-end production by compiling data from all the data sources used during production. If you use an MES, Digital Twins can pull in MES data alongside other data sources—raw material information, financial data, or even the process data from a single distillation still—seamlessly. The ability to access and utilize this level of product traceability can lead to groundbreaking discoveries and opportunities.
This level of granularity is nearly impossible for an MES system to provide. Yes, an MES makes it possible to collect a lot of data, but most spirit and beverage manufacturers have too much data. The issue they face is having the right tools to validate the data, analyze data, understand data, and draw relationships between different data sets to make meaningful discoveries.
For example, let’s assume your spirit company worked with Braincube to build a Digital Twin of one of your distillation stills. Using the data from the distillation column, teams can leverage advanced analytical tools to understand which process parameters are impacting yields or resulting in unnecessary energy consumption.
One such tool is Braincube’s Advanced Analysis application. This app empowers process experts to improve production by equipping them with self-service AI that builds upon their implicit knowledge. The app helps teams discover how different variables impact production so they can solve complex issues or hit business objectives.
Production batches will always have some variability. The key to reducing variation is identifying and isolating the inputs that are responsible for generating specific (and, in most cases, undesired) outputs causing variation.
Braincube’s proprietary CrossRank AI, which is utilized in the Advanced Analysis application, is capable of isolating specific variables that have the greatest impact on achieving your set objective. The app also provides recommended settings based on what you want to achieve, making it even easier to implement changes that drive progress forward. With this knowledge, teams can continuously improve processes like distillation.
The app extends what’s possible with root cause analysis. Not only can the app help perform root cause analysis, but it also provides teams with the solutions to avoid future problems, improve existing bottlenecks, and fix what isn’t working. These discoveries would be impossible with AI.
Even if some dirty data sneaks into your calculations, AI makes it easier to overcome this possible barrier to discovery. AI can compute 200 quadrillion calculations per second. At this volume of data calculation, the algorithm compensates for data anomalies that may exist in your MES or historian.
Digital Twins, plug-and-play Business Intelligence applications, and autonomous technologies like AI all play a role in empowering employees to get the most out of their intrinsic production knowledge. With these (and more!) advanced IIoT solutions, beverage manufacturers can level-up their quality control efforts and outcomes.
Today’s Industrial Internet of Things (IIoT) tools and technologies put valuable data into the hands of your employees so they can work their magic. Here are some key opportunities for spirit manufacturers.
Improved access to real-time data enabled a global CPG company to improve efficiency, uptime, and optimize its resources. Not to mention, they improved their OEE by over 30%.
Turn production data into your competitive advantage. See how Braincube’s IIoT Platform can help you improve traceability and find new success.