Revolutionize your paper manufacturing with AI-driven optimization. Enhance efficiency, cut costs, and achieve autonomous operations like industry leaders Arjowiggins and Oji Paper. Embrace the future of smarter production!
Learn more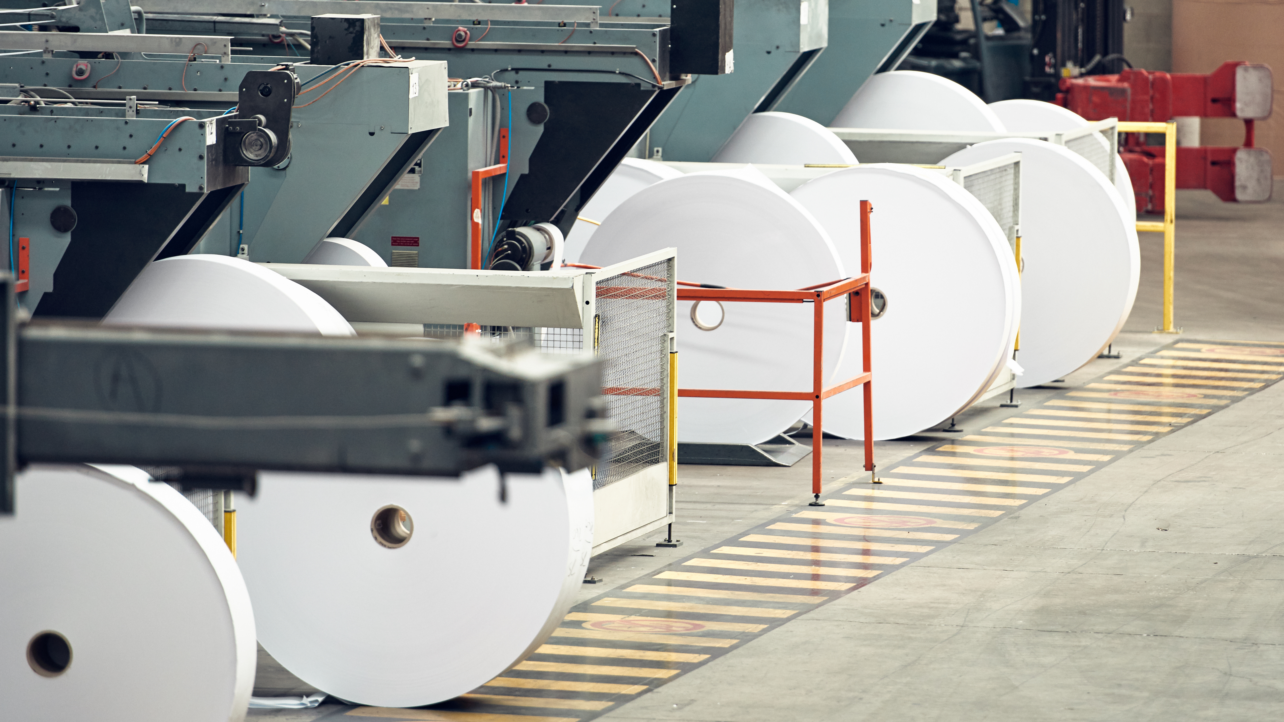
A digital twin of your manufacturing process, contextualized by individual products, can help identify process optimizations, reduce costs and waste, and improve quality and sustainability.
As digital twins have become more crystalized across manufacturing, evolutionary concepts like the digital thread have emerged. In fact, searches for the digital thread have risen 433% since 2015. Research firms are stating that digital threads are ‘the next big thing’ for manufacturing.
But what exactly is a digital thread? How are digital threads different than digital twins? Do you need digital twins before you have a digital thread?
Like many hyped innovations, the concept or theory behind digital threads is often easier than the execution. In this article, we break down some of the key takeaways about both digital twins and digital threads in manufacturing, including key differences between them.
In the simplest terms, a digital twin is a digital replica of any production outcome, system, or asset. These digital representations are updated using real-time data from sensors, making it possible to simulate what’s happening on the shop floor in a digital environment.
A Braincube-powered Digital Twin encompasses and contextualizes the entire process flow, accounting for all production variables. This includes system data, supplier information, sensor data during production, raw materials, quality data, and more. Exact lag times are automatically added to all of this data for the most accurate, relevant, and comprehensive digital twin.
By associating production data with specific process stages, Braincube’s Digital Twins provide you with a full production blueprint of every product, serial number, or batch coming off the line. Data sources are continuously aggregated and contextualized by both timestamp and by-product reference. As a result, data is formatted into a dynamic digital replica of the exact production process.
Digital Twins serve as the gateway to self-service analytics, data visualization, custom data science models, and other application use cases across the entire manufacturing thread. Since data is automatically consolidated, cleansed, and formatted into a usable format for teams, data is always readily available for teams to use for problem-solving.
Typical digital twin use cases include uncovering root causes, identifying and preventing defects, optimizing processes, and expanding predictive maintenance strategies. Digital twin data can be used to:
A manufacturing digital thread is designed to expand upon a digital twin. Put simply, the digital thread captures digital twin data as they evolve.
As manufacturers evolve their processes and their digital twins adapt to new settings or recipe changes, the digital thread encapsulates the link between these evolutions. For example, how did your product quality, production cost, or energy consumption evolve? What progress did you make? The digital thread in manufacturing is meant to measure your progress and improve your production process over time.
For example, digital threads can help manufacturers uncover the precise temperature in a shipping container, the ideal store placement for the highest selection, and, even better, inform the value stream.
Digital threads in manufacturing are not limited to a specific industry. According to Gartner analysts, 70% of the top 20 global consumer goods companies will include consumer feedback in their customer experience strategy. This type of hyper-personalization is made possible in part by digital thread technology.
The best way to capture the difference between digital twins and digital threads is to think about the data captured in each database. Digital twins primarily deal with a product’s production cycle: digital twins capture manufacturing data related to how a product is produced.
Digital threads enable teams to capture and analyze data from a product’s entire lifecycle. What supplier information can you capture before a product is made? What happens to a product after it leaves the factory? These data points inform digital threads, filling in the gaps on either end of a digital twin.
In general, digital twins are used for process optimization. The value of a digital twin increases with time as new data comes in. Digital twins use historical data to help you understand how to optimize now.
A digital thread brings in additional data points from pre-production through the end of life. Digital threads use data over a product’s lifecycle time to help you further optimize product quality, production efficiency, and other KPIs.
Digital twins provide a virtual replica of physical processes but their scope is focused to include manufacturing data. A digital twin can help you answer how was something made at a specific point in time.
Digital threads expand to capture data over time, often adding additional data sources. For example, a digital thread would include pre-production information like the supplier, OEM data, blockchain, or point of sale information. Digital threads enable manufacturers to understand the impacts on quality, energy, etc. after production takes place.
One of our automotive customers is leveraging VINs to track product components of their vehicles over time. Their Braincube-powered digital twin data is built by VIN, enabling them to they have started to track the car’s lifecycle.
For example, a digital twin shows a car’s paint quality at the time of production. A digital thread can add additional lifecycle information, such as paint quality correlated with customer satisfaction levels, maintenance paint orders, and other types of depreciation.
Capturing and analyzing product lifecycle data via digital threads offers manufacturers the opportunity to further optimize aspects of production. For example, digital thread data can inform changes to make an optimal paint recipe that meets current specs and has lasting quality.
Digital thread data can even expand into carbon reduction initiatives, quality control, sustainable sourcing, and other key strategies to help manufacturers make the right product for their customers.
Historically, digital threads for manufacturing have been used in heavily regulated industries like aerospace and defense. However, we’re seeing a shift into other industries, including food and beverage manufacturing.
In food and beverage production, taste, quality, and volume are key. For example, an innovative food manufacturer that we work with wanted to tie point-of-sale data back to their innovation hub. This company produces several food products with different flavors, many of which are seasonal.
They want to use their point-of-sale data to trace how recipe changes affected their customer ratings. This will allow them to source the most effective raw materials and ensure the highest level of customer satisfaction.
Further, they are looking at the start of the process too. They are linking back customer satisfaction data to their supplier information of each batch. Did different supplier ingredients yield the same level of satisfaction? Did the consumer even notice? Is it worth diversifying suppliers, offering premium, basic, or some other level of product? Having data that connects innovation through sales data offers new opportunities for optimization for manufacturers around the world.
The value of a digital thread in manufacturing is nearly unfathomable. Because it is designed to capture data that leads to better resourcing and cost control, it is difficult to put a hard number or estimate a projected return on investment.
Imagine if manufacturers could easily interconnect point-of-sale data, engineering specs, and production details into an intricate package of information. Having this data organized and updated would bring a new layer of intelligence. It could help shorten time-to-market, improve people organization, and even optimize maintenance planning.
In today’s world, consumers expect hyper-personalization more and more often. They want to select the color of their shoes, the color of the thread in their car seats, or even the flavor in their soda. When offering personalization, the consumer can have an excellent experience, but that personalization data may not make it back to the manufacturer. Digital threads are trying to close this feedback loop.
Building a digital thread is not something that happens overnight. Building and executing such a heavy lift requires a highly mature IT infrastructure and data governance framework.
Digital threads expand to capture data over time and often add additional data sources such as pre-production information like the supplier, OEM data, blockchain, or point of sale information.
Regardless of where you are on your digital transformation journey, all of these technologies are moot without the right data. Without the perfect data—meaningful and organized data—you won’t have concrete results to enhance your production process. Braincube provides the tools you need to break through Industry 4.0 with the right tools, data, and services.
Digital threads are another piece of the Industrial Internet of Things. Subscribe to see more content related to Industry 4.0, or jump right in with a self-guided tour of Braincube.
Digital twins can make a big difference in helping your manufacturing company push through data fatigue and turn data into your competitive advantage. But what exactly are manufacturing digital twins, and how are they used?
Initiating a digital transformation strategy is a big step, and our company needs a long-term plan for a successful transformation. Learn the five key pillars to build a strong foundation for your company’s Industry 4.0 strategy from the ground up.
Digital twins can be built for any part of your process or any physical entity of your production process. In this article, we unpack a few different types of digital twins found in manufacturing, including the pros and cons of each type.