Revolutionize your paper manufacturing with AI-driven optimization. Enhance efficiency, cut costs, and achieve autonomous operations like industry leaders Arjowiggins and Oji Paper. Embrace the future of smarter production!
Learn more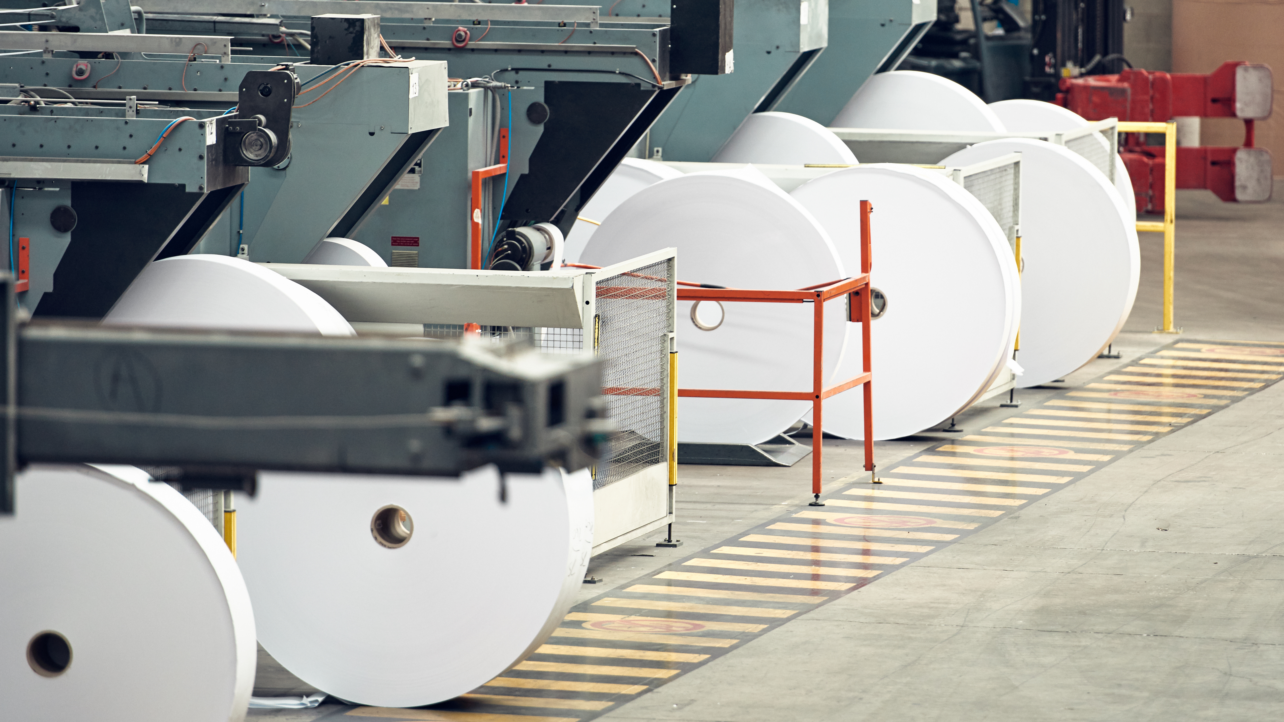
In many ways, scaling digital transformation to more manufacturing facilities is no different than implementing a digital transformation initiative. You’ll still need to motivate employees to work in new ways, hit adoption or usage targets, and make sure projects don’t fizzle out with disinterest.
Even with these similarities, you can scale your digital transformation efforts easier with a few internal changes.
Openly collaborating with your vendors makes implementing—and scaling—digital transformation tools easier for everyone involved. Including your solution partners in your journey puts IIoT vendors in a proactive position, enabling them to guide you in the right direction as you scale your digital transformation strategy over time.
Your partners can help you get unstuck if you hit roadblocks along the way. With years of experience onboarding new businesses, your software vendors have likely seen certain problems before. Whether you run into technical issues while rolling out at a new facility or need help training new teams, vendors can offer up ideas, processes, or frameworked templates to keep you on track.
For instance, Braincube has partnered with leading pulp and paper manufacturer, Sappi, on scaling their digital transformation globally. One of Sappi’s key discoveries was that 80% of the legwork involved building an accurate Digital Twin. If tags are not up to date, the right data flows—and therefore the correct information—can not get to the right people. In other words, the data may not truly align with what is actually happening on the shop floor.
“Data integrity is key to ensuring credibility and momentum when scaling a solution to other production lines, factories, or geographies,” said Joanne Boyd, Global Service Manager for Advanced Analytics at Sappi.
As a result, Sappi knew they wanted their internal teams involved with the creation and ongoing improvement of their Braincube Digital Twins. They knew that having hands-on involvement in the Digital Twin creation would ensure that everything was up-to-date and working correctly.
“We wanted to develop in-house capability to be able to continuously improve the Digital Twins,” said Boyd. “Things change all the time. We want to proactively ensure that our Digital Twins and analytic solutions are a true reflection of plant operations.”
Braincube’s hands-on consulting played a key role in getting Sappi’s teams up to speed with assigning the correct data tags and leveraging their existing tag structure. Partnering closely with their Braincube team throughout the scaling process has made a key difference in helping them stay on track to meet their ambitious goal: building ~165 Digital Twins across 18 mills within a 3-year time period. Their internal knowledge is heightened by Braincube’s IIoT Platform framework, making it possible for them to have greater autonomy as the company grows, changes, and makes new discoveries.
Internal transparency, especially into the efforts of different teams, is another key aspect of scaling digital transformation to more sites. Seeing what colleagues are working on (no matter where they are located) is an excellent way to find common ground and drive improvements in your own facility. Even if teams don’t collaborate directly with each other across geographies, they can still gather insights and ideas that can be applied in their region or department.
Visibility and transparency are key drivers for our Industry 4.0 initiatives. They promote reusing solutions and lessons learned.
— Joanne Boyd, Global Service Manager for Advanced Analytics at Sappi
Sappi’s corporate team credits their organizational structure for their success as they scale their digital transformation efforts across more sites globally. Sappi’s leaders invested in an innovation hub solution that enables global visibility into all Advanced Analytics initiatives. This visibility promotes solution scaling across the organization.
“Every single data science initiative related to our Braincube Digital Twins is captured into the innovation hub, enabling everyone across the organization to view and contribute,” said Boyd. “Anyone within the organization can contribute by capturing an ‘idea’ which proceeds through various stage gates starting with evaluation, proof of concept, and, when feasible, to operationalization.”
The key differentiator for Sappi is that anyone else at the company, no matter where they are located, can see these projects. Access to these ideas, even if they aren’t fully formed, inspires other leaders to experiment and try new projects, building upon the collective mind sphere.
“Visibility and transparency are key drivers for our Industry 4.0 initiatives. They promote reusing solutions and lessons learned,” added Boyd.
The same goes for sharing wins. Internal teams can be the biggest cheerleaders and advocates for a given project, tool, or methodology. Showcasing positive results from one facility amongst your other facilities is a great way to spark conversations, show what’s possible, and gather buy-in from teams that may lag behind on their enthusiasm to get started.
One of the number one reasons why digital transformation efforts don’t deliver the results they promise beyond the POC stage is unsuccessful change management. Change management is a vital aspect of digital transformation and it is even more important as you scale. Weaving an ownership mindset into your employees is not an easy task, especially if you are trying to overcome “the way things have always been done.”
One way to get shop floor buy-in is to give employees greater autonomy with their digital transformation projects. If a plant’s digital transformation project is the responsibility of teams working on the ground at the facility, there is a higher likelihood that employees will want to be involved. Leaders can promote and encourage this ownership mindset by assigning Industry 4.0 champions at each facility.
These champions can be responsible for a variety of tasks related to training, rollout, project management or selection, and tracking success. Here at Braincube, we have seen improved adoption and usage rates—and ultimately, results—when someone at the facility (not a corporate leader) is in charge of making sure a tool is used and given ample resources to be successful.
There are a few reasons why this is the case. Plant teams, including operators and engineers, often prefer working closely with someone at their facility instead of intermittent communications from someone at the corporate office. Local champions are the most familiar with a given facility’s inner workings, including the biggest challenges and production nuances. These insights are immensely valuable when deciding what projects to start, if a process change makes sense to implement, and the plant’s capacity for trying new things.
At Sappi, their digital transformation “champions” are usually technical managers or production managers. These individuals really “promote and drive” the Industry 4.0 initiatives at their facility, according to Boyd. She also emphasizes that assigning leaders at each plant can make a big difference in a tool’s adoption rates and usage.
Sappi’s corporate leaders meet regularly with local plant champions to get a pulse on their digital transformation projects. Each site champion and regional manager are responsible for presenting their facility’s projects, usage stats, and outcomes at these quarterly meetings. This accountability emphasizes a champion’s importance (as well as their team’s importance), motivates them to set and achieve goals, instills pride in successful projects, and provides them an opportunity to prove themselves.
When possible, emphasize that facilities aren’t competing with one another. Focus on bridging communications and shared wins between plants, building stronger collaboration between different facilities in a way that helps everyone grow and level up.
Like most new projects, a lack of time is still the biggest bottleneck facing operations teams tasked with continuous improvement. Corporate leaders must find a way to give plant champions (and operations teams) ample time to work on Industry 4.0 projects—whether it’s set up, technical training, upskilling, or analysis. If new tools or projects are tacked onto a growing list of responsibilities without freeing any time, it will result in strained employees and greater resistance to digital transformation.
“The challenge is to enable employees by introducing new tools and ways of working, on top of a very busy schedule,” said Boyd. “Corporate leaders and managers need to support and invest in training and find ways to embed the use of contextualized data into day-to-day operations.”
An easy way to give employees time—both to learn new technology and to complete their existing tasks—is to build a robust training program. Ideally, training programs are developed (or at least coordinated) at the corporate level instead of requiring each facility to figure out their own training.
The goal of your training program should be to give employees hands-on experience with a new tool and the opportunity to continue using the tool outside structured training. As Sappi rolled out Braincube to new facilities, they discovered that short training sessions with smaller groups of employees are the most effective for scaling their digital transformation initiatives.
“The smaller, focused training groups give us quicker wins,” said Boyd. “These success stories play a key part in rolling out the software to the rest of the people at a plant. If you can’t achieve wins early and show others the power of a given tool, adoption tends to fizzle out. The right training has made a big difference in which mills are successful and which mills lag behind.”
If you can’t achieve wins early and show others the power of a given tool, adoption tends to fizzle out. The right training has made a big difference in which mills are successful and which mills lag behind.
— Joanne Boyd, Global Service Manager for Advanced Analytics at Sappi
Shorter, hands-on training sessions also make it easier for engineers to take the time. Running training sessions more frequently gives operations teams the opportunity to use what they learn and implement their new skills right away. If training sessions are spaced out too much, employees may forget what they’ve learned. This continuity gap makes it harder to pick new skills back up at future training sessions and doesn’t reinforce a tool’s usage in an organic way.
Bringing your training efforts more into the corporate office also arms teams with a strategic game plan for future rollouts. As initiatives are rolled out to new facilities or teams, corporate teams can build upon previous training sessions to improve scaling initiatives. Improving your roll-out framework results in a snowball effect, making each new plant roll-out more streamlined and efficient than the next. This is far more effective than having each facility start at square one while simultaneously making the most of your learnings
Corporate teams can reinforce a tool’s usage by helping champions make sure the tool is used as often as possible. The more hands-on experience teams have with using a tool, working through a new procedure, or seeing the successes of other facilities, the more inclined they will be to start working in a new way.
Do your best to structure KPIs, team goals, and other initiatives around new 4.0 tools and methods. This may include using a tool directly or solving problems in a way that incorporates a new way of working.
“You have to structure the organization in such a way that gives people time to learn, use, and engage with the product,” said Boyd. “Make the new tool part of someone’s daily role instead of something over and above what they’re already doing.”
Sappi’s leaders have taken this approach even further by instilling a commitment to their enterprise Industry 4.0 strategies at the corporate level. The executive team has created a new global department dedicated to the training, development, and support of advanced analytics initiatives thereby ensuring teams are enabled and invested.
Sappi’s leaders have strategically prioritized digital transformation initiatives, which further emphasizes the strategy’s importance in the day-to-day workflow. Boyd credits this “top-down filtering” of their strategy as a key reason for their “digital transformation culture change” throughout the organization.
If you want to effectively scale your digital transformation efforts to other facilities, your best tools are the ones you’ve already got in your pocket. Take learnings from your initial IIoT implementations—both the good and the bad—to guide future rollouts and adoption.
The more buy-in and assistance you can get from your executive teams, both in terms of resource allocation and setting overarching company goals, the easier it will be to get new facilities on board. When in doubt, lean on your third-party vendors for support, knowledge, and training advice.