AI-powered automated operations have revolutionized various industries. However, to truly reap the benefits for both people and the environment, it is crucial to put these changes into practice. These practical implementations can unlock the full potential of autonomous manufacturing.
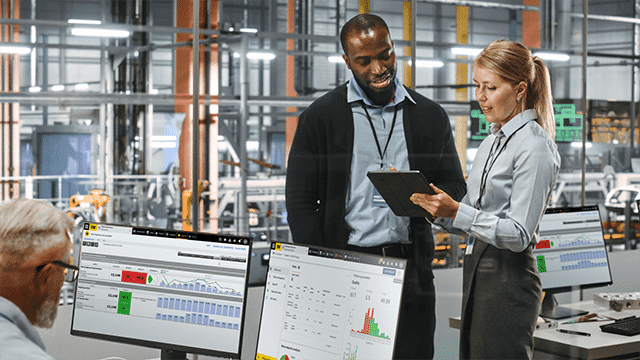