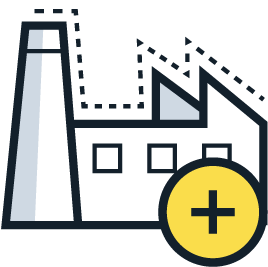
Cargill’s data analysis is 50% faster with Braincube
Cargill wanted to spend less money operating their oil boiler while maintaining steam output. Cargill’s internal analyses had yet to significantly impact the boiler’s efficiency because they couldn’t identify the optimal set points to improve boiler efficiency without decreasing steam output.

Learn how Cargill significantly saved in boiler operating expenses and increased weekly recipe production by 400% after using Braincube for only one year.
Why Braincube?
Not all IIoT Platforms are created equal. Braincube was designed by manufacturers to meet the specific challenges of today’s competitive manufacturing world.
Solutions for Your Needs
Whether you’re looking for an IIoT Platform, Cloud, or Edge solution, we can help you solve your manufacturing challenges.
Expand your Knowledge
Not sure where to start on your Digital Transformation journey? Brush up on the basics or learn about the latest Industry 4.0 trends in our Resources section.