Handling Complexity: Why Agility is the Key to Industrial Leadership
For over a century, Aubert & Duval has been a global leader in supplying superalloys, titanium, aluminum, and other high-performance materials to the aerospace, defense, and energy sectors. With 4,100 employees spread across 10 production sites, the company owns a unique expertise to produce ultra-complex materials that are far from being ordinary materials. They have to resist extreme temperatures, corrosive environments, and strong mechanical stress—all while ensuring uncompromising quality.
At Aubert & Duval, precision is paramount. Even the smallest process deviation can trigger defects, compliance issues, and costly rework. When the company first turned to Braincube, the focus was solving critical quality and precision issues that traditional methods couldn’t address.
At the same time, Aubert & Duval’s operates in an industry where market conditions change very quickly. Today’s focus might be reducing energy costs, while tomorrow it’s ramping up production to meet rising demand from clients like Safran or Airbus.These cycles directly impact how operations need to be managed, requiring flexibility and agility in production strategies.
Recognizing broader potential, Aubert & Duval expanded their vision for Braincube’s Productivity Management System beyond fixing immediate pain points. They challenged the system to create a manufacturing environment that could continuously improve performance, reduce waste, and adapt to evolving business priorities—without adding operational complexity.
From Variability to Stability: The First Step to Productivity
At the Ancizes plant, one of Aubert & Duval’s largest production sites, for years manufacturing teams had relied on manual adjustments, post-production reports, and experience-based decision-making to maintain quality. Without a clear, real-time view of process conditions, optimizations were slow and inconsistent. While the industry was shifting within a more and more competitive landscape, the old way of gut feeling and trial-and-errors wasn’t enough anymore.
To stay ahead, Aubert & Duval needed a deeper level of process intelligence—one that didn’t just tweak existing workflows but fundamentally challenged the status quo.
That’s where Braincube’s Productivity Management System came in. Instead of focusing on isolated process improvements, Aubert & Duval used a system-wide methodology to drive productivity across all levels of organisation—from operators and engineers up to plant managers and corporate leaders.
By integrating Braincube’s Productivity Management System, teams at Ancizes moved from reactive adjustments to proactive, continuous process optimization:
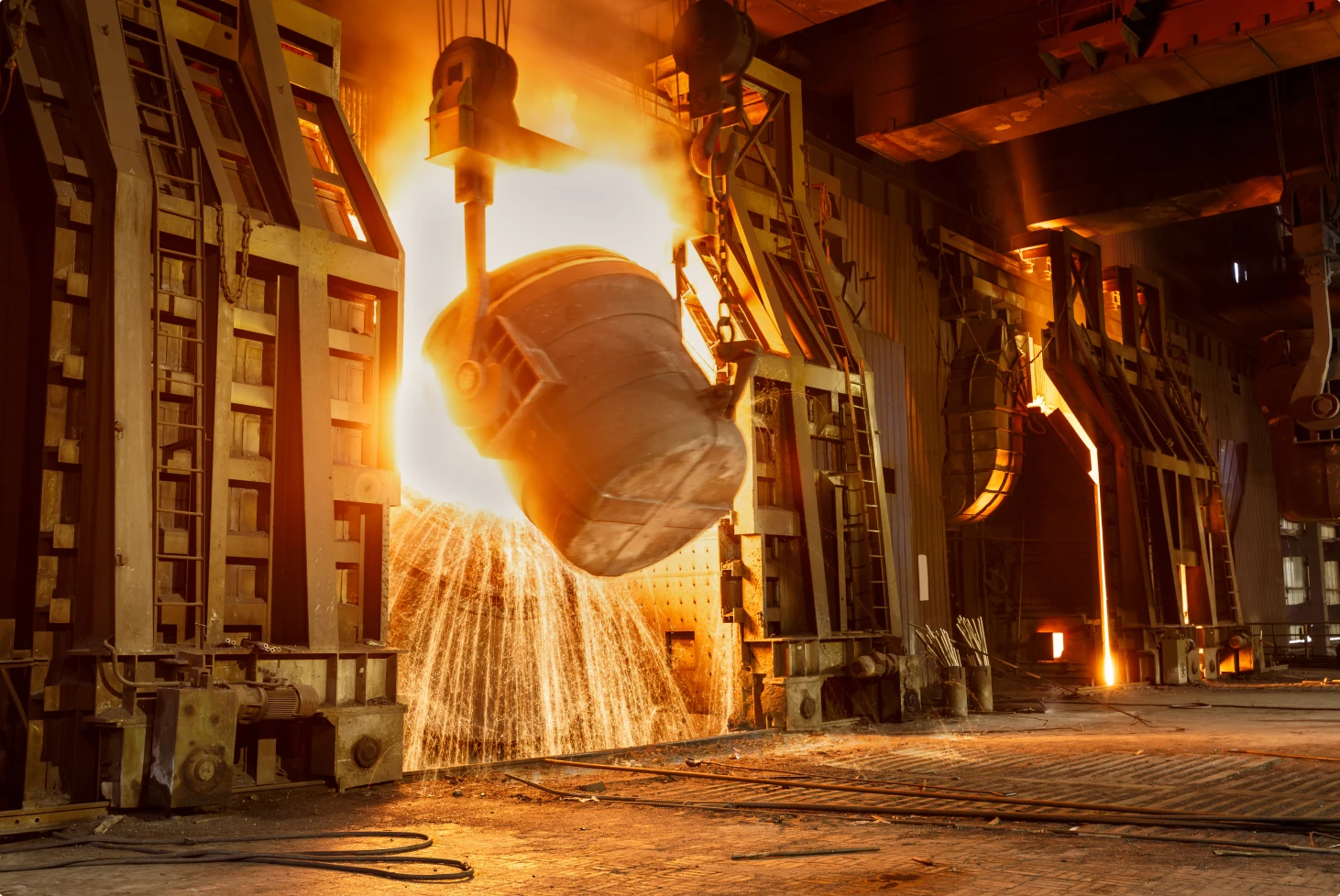
- Operators stopped firefighting and started making real-time adjustments based on live process conditions, reflected through 130 real-time dashboards,
- Engineers, powered by CrossRank AI, could easily identify correlations between variables that had gone unnoticed for years, allowing them to fine-tune parameters before quality issues occurred.
- Plant managers gained visibility into site-wide performance and instant productivity gains, making it easier to follow-up progress and standardize best practices across shifts.
- Corporate leaders could track KPIs across multiple sites, accelerating data-driven decision-making at scale.
Within several months, the impact was measurable:
- Defect rates dropped by 18%, thanks to optimized process parameters.
- Process stability improved by 32%, ensuring a more predictable, repeatable production cycle.
The shift was going far beyond simple optimisation – it changed how decisions were made, how teams worked together, and how productivity was measured.
From Hidden Waste to True Potential of Energy Efficiency
With quality and production stability under control, Aubert & Duval turned its focus to another major factor in industrial productivity: energy.
Energy was one of the company’s largest operational costs, but it wasn’t optimized so far. Engineers had the tools to track global energy consumption, but they didn’t know exactly if the theoretical energy consumption was corresponding to the real consumption needed for each process. Energy waste wasn’t closely monitored but the corporate team knew there was a huge potential for improvement. That’s how they set an ambitious target to reduce energy consumption by 15% without impacting production or quality.
Braincube proposed to use a different approach while treating energy not as a fixed cost, but as a production variable that could be optimized—just like quality and production stability.
With Braincube’s advanced energy dashboards, teams could now see, in real time, exactly how each machine, process, and production batch impacted gas and electricity consumption.
The first findings with Braincube revealed significant sources of the hidden waste:
- Furnace loads weren’t optimized for batch size, leading to excess gas consumption.
- Certain heat treatment cycles were running longer than necessary, adding unnecessary costs.
- Idle equipment was consuming power during non-peak hours, creating hidden waste.
Instead of relying on generic energy reduction strategies, teams had actionable, plant-specific insights to work with.
The impact? Better control, better savings, and faster decision-making:
- Gas consumption dropped by 19%, simply by optimizing furnace usage and cycle times.
- Electricity use decreased by 3%, through better load balancing across shifts.
- Operators now had real-time visibility, allowing them to adjust power-intensive processes in the moment, not after the fact.
By integrating energy efficiency into daily operations, Aubert & Duval transformed a major cost factor into a new source of productivity gains.
From Optimisation to Strategic Agility: Bringing Productivity to Every Plant
As results accumulated, Aubert & Duval scaled this approach across other sites—ensuring that every plant, every process, and every team could maximize efficiency with the same level of precision.
With Braincube embedded into daily operations across seven sites, Aubert & Duval teams now had the tools to make faster, smarter decisions at every level of the organization—from operators on the shop floor to corporate leadership.
- For executives and plant managers, agility was no longer a challenge. They could now adjust production strategies on the fly—whether that meant scaling output to meet surging demand or fine-tuning processes to drive cost reductions.
- For engineers and quality teams, real-time process control has eliminated guesswork. By continuously refining production setpoints, they ensured greater process stability, higher precision, and reduced defects—without adding complexity to workflows.
- For energy and operations teams, efficiency became a new performance lever. Braincube made it possible to track and optimize energy use in real time, aligning energy consumption with production needs instead of relying on broad reduction strategies.
As their Head of Digital Transformation observed: “Braincube became part of how we operate. Whether it’s optimizing raw material usage, reducing production bottlenecks, balancing machine loads, or cutting energy costs, the logic is the same: operational intelligence allows us to anticipate, optimize, and accelerate performance at every level.”
What began as a project to stabilize process conditions has evolved into a company-wide culture of Total Productivity—integrating Braincube into daily operations and decision-making at every level, while uncovering new efficiencies year after year.
Even after 14 years of daily Braincube usage, Aubert & Duval continues to push the limits of industrial productivity—finding new gains, new efficiencies, and new ways to drive operational excellence forward.