Navigating Complexity in a Rapidly Changing Tire Market
The tire industry is changing fast. As more people buy SUVs, electric vehicles, and commercial trucks, the demand for larger, high-performance tires is on the rise. Meeting this demand isn’t simple—making each tire involves controlling thousands of variables. If something goes off track, the consequences cascade into more defects, wasted materials, and slower production lines.
Market volatility compounds these challenges. Fluctuating raw material prices, shifting consumer preferences, and changing economic conditions create unpredictable demand patterns. One month, orders can surge;, while the next, they can suddenly drop. This reality requires manufacturers to build agility into their production strategies, balancing throughput with cost-reduction with cyclical demand.
For Tire Giant, these industry trends manifested as specific internal challenges:
- Rising production costs from volatile raw material and energy prices.
- Pressure to maintain high product quality despite increasing process complexity.
- Shifting customer demands requiring faster production adjustments.
- Regulatory pressures to reduce waste and improve sustainability.
- Difficulty comparing performance across plants due to inconsistent data systems.
These combined pressures highlighted the need for a solution that could boost productivity, improve agility, and ensure consistent product quality across all operations.
Why Productivity Is the Missing Piece for Tire Manufacturers
Tire Giant’s production lines operate at remarkable speeds—some facilities produce up to 40 tires per minute. Each manufacturing stage generates massive amounts of data, from material preparation to final inspection. However, this valuable information was scattered across disconnected systems: MES handled production data, ERP systems managed planning, and local spreadsheets documented daily operations.
This siloed approach made it difficult to gain a complete view of production. Engineers spent hours gathering data to investigate issues, while operators often relied on experience instead of real-time information. Corporate teams struggled to benchmark plant performance, making global alignment challenging.
Although established methods like Six Sigma and DMAIC had delivered improvements in the past, they had reached their limits. With thousands of variables and rapidly changing production requirements, Tire Giant needed a faster, more comprehensive system that could:
- Unify data from all systems for a single view of production.
- Identify the variables with genuine impact on efficiency and quality.
- Enable faster, better decisions at every level of the organization
- Ensure operational agility in a dynamic market
Braincube’s Productivity Management System emerged as the solution to achieve these goals, providing the visibility and actionable insights teams needed to act quickly and confidently while transforming operations without interruption risks.
From Complexity to Total Productivity
Tire Giant selected its French plant as the proof of transformation site because of its strategic importance in producing large tire sizes for premium vehicles. The plant faced challenges as older equipment wasn’t designed for the size and weight of newer models, creating significant inefficiencies. Operators frequently needed to halt production for setting adjustments, and with fragmented data systems, identifying preventive measures was a slow, manual process. At high production speeds, even minor inefficiencies caused substantial operational and financial impacts.
This location offered the ideal balance—complex enough to demonstrate meaningful results, yet important enough that improvements would deliver significant impact. Addressing these issues promised quick wins to showcase Braincube’s potential while creating a scalable model for global deployment.
Before implementing Braincube, teams faced daily operational hurdles:
- Engineers spent hours sifting through scattered data to investigate issues.
- Operators relied on intuition to make adjustments, risking inconsistent results.
- Corporate teams lacked timely insights into plant performance.
How Tire Giant Transformed Operations
Braincube worked closely with Tire Giant’s teams to transform operations through three key components that addressed critical challenges and delivered measurable improvements.
First, Product Clones tackled the issue of disconnected data. Tire Giant previously struggled to understand how production settings and raw materials affected the final product, as information was scattered across multiple systems. Product Clones aggregated this data, providing a clear, step-by-step view of each tire’s production journey.
Next, CrossRank AI helped make sense of the thousands of variables influencing efficiency and waste. Analyzing these variables manually made it nearly impossible to determine which factors truly influenced production. CrossRank AI continuously analyzed all variables in real-time to highlight the most critical process parameters, providing engineers with optimal settings and reducing problem-solving time from hours to minutes.
Lastly, Digital Assistants addressed delays in accessing vital information. By delivering real-time guidance to operators, providing detailed metrics to engineers, and offering performance updates to corporate leaders, Digital Assistants ensured everyone had the information they needed when they needed it. Operators could act immediately to maintain optimal production conditions, while management teams made faster, better-informed strategic decisions.
Together, these solutions replaced guesswork with precision, enabling Tire Giant to shift from reactive problem-solving to proactive process management.
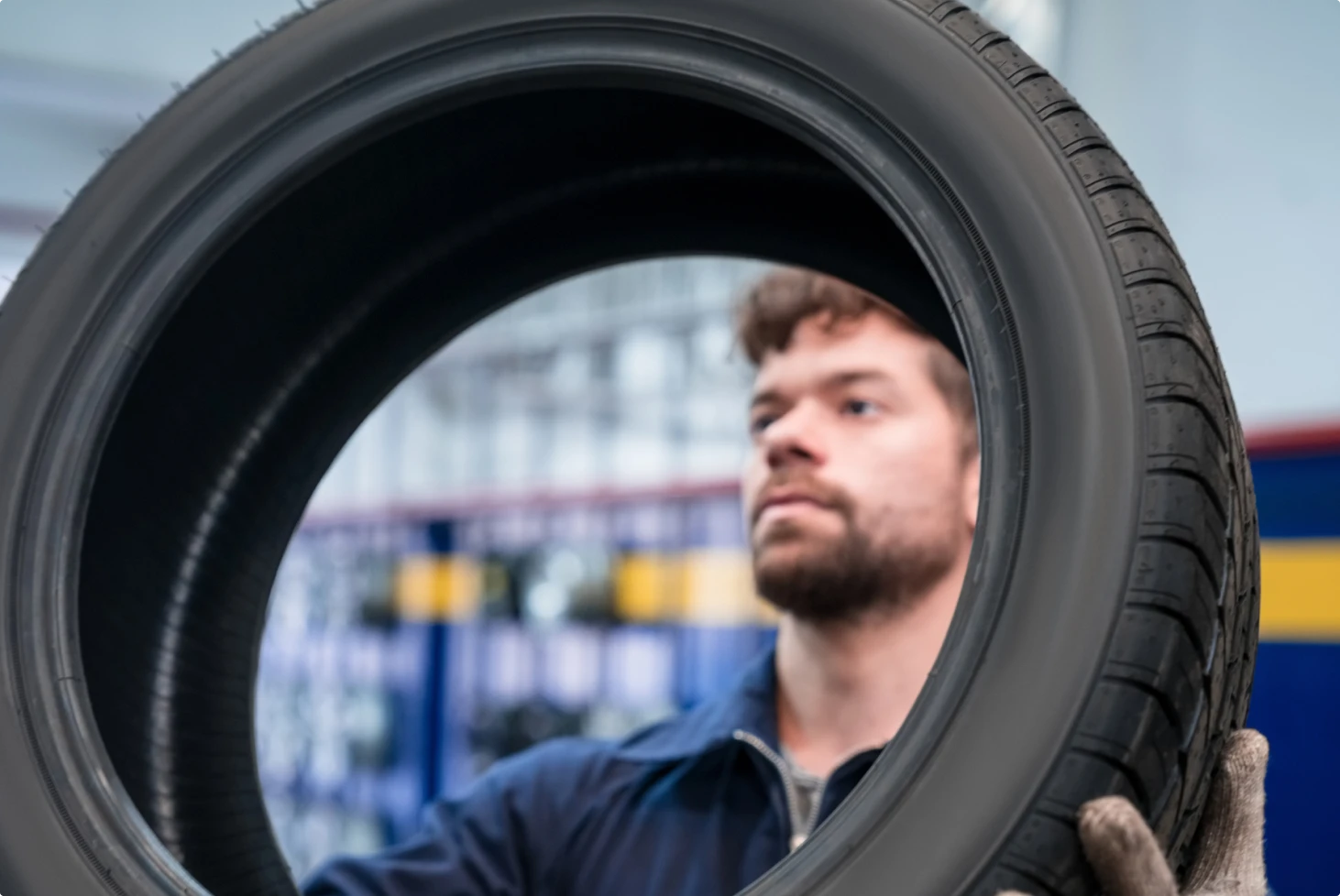
From Insight to Impact: Achieving Fast, Measurable Gains
Tire Giant’s French plant experienced a deep operational shift after implementing Braincube and achieved a breakthrough in productivity gains in just several months.
Quantifiable Gains:
- $1M in annual savings through optimized production settings and faster adjustments.
- 35% reduction in waste as a direct result of improved process efficiency.
- 90% less time spent on manual data processing work, freeing up teams to focus on improvements.
Transformational Results:
- Real-time adjustments helped operators keep production running smoothly.
- Better collaboration between operations, engineering, and management teams.
- Improved production agility, enabling faster adaptation to demand fluctuations and process variability.
Scaling Success Across Global Operations
The pilot plant’s success provided a proven, replicable model for global deployment. Tire Giant expanded Braincube to over 60 facilities worldwide in less than four years—an impressive achievement given the complexity of data systems and the unique conditions of each production site.
Success factors of a rapid global rollout:
- Implementing a global product tagging system to ensure consistent data structure across all plants.
- Braincube benchmarking capabilities allowed plants to compare performance and adopt proven best practices.
- The scalability and adaptability of Braincube’s system, which easily adapted to local infrastructure without extensive IT overhauls.
- Unified data access to help teams worldwide to better collaborate on data and make faster decisions company-wide.
Thanks to these efforts, the productivity gains initially achieved in France have now been replicated across all of Tire Giant’s plants worldwide. Each facility is making faster data-driven decisions, operating with higher process consistency, and realizing significant improvements in productivity.
Tire Giant’s Next Productivity Milestones
Tire Giant’s goal wasn’t just to cut waste—it was about making production more efficient, responsive, and cost-effective. Benefiting from better process visibility, costs and quality control, and faster decisions, the company is well-positioned for upcoming market changes.
Building on achieved gains, Tire Giant continues working on:
- Strengthening corporate OKR visibility to align plant operations with strategic goals.
- Continuing to meet evolving demands for electric vehicles, SUVs, and sustainable tire solutions.
- Expanding global benchmarking initiatives to accelerate best practice adoption.