Empowering a Global Team for Sustainable Manufacturing Gains
Sappi, a global leader in woodfibre-based products, is no stranger to innovation. Serving over 150 countries, their operations span specialty papers, dissolving pulp and biomaterials. Despite some local successes, their fragmented systems and disconnected data limited their ability to scale solutions and achieve global excellence.
By 2019, each region—South Africa, Europe, and North America—relied on isolated tools and processes, leading to inconsistent standards and untapped opportunities.
“Every plant had its own way of working with data,” recalls Joanne Boyd, Global Service Manager of Advanced Analytics. “This inconsistency prevented us from achieving the unified approach we needed.”
To overcome these challenges, Sappi sought a system that could seamlessly connect people, processes, and data—turning complexity into clarity. Enter Braincube.
Turning Complexity Into Clarity
Disconnected systems left teams bogged down in data preparation. “Building product clones consumed 80% of our digitization effort, slowing progress,” says Boyd. “We needed a more efficient way to scale across the organization.”
The challenge: turn fragmented data from dozens of systems into actionable insights for better decisions, problem-solving, and innovation.
Braincube’s Product Clones provided a transformative solution. These dynamic replicas unified siloed data from multiple systems, formats, and time series, empowering engineers, operators, and executives to access reliable insights and make confident, informed decisions quickly.
A Culture of Data-Driven Excellence
The shift wasn’t just technical—it was cultural. Braincube’s tools empowered engineers and operators to independently analyze and act on data, reducing reliance on data science teams.
“Braincube put the right tools in the hands of those closest to the problems,” Boyd explains. “Suddenly, our teams were solving issues that had lingered for years—and doing it faster than we thought possible.”
Collaboration and training created early wins that inspired teams across plants. Braincube’s frameworks ensured data accuracy, while hands-on support helped engineers adopt the new approach.
“One team’s success inspired others,” Boyd adds. “The tools were intuitive, but the cultural shift was what really unlocked our potential.”
Transforming Potential Into Performance
In two years, Sappi turned disconnected efforts into a unified strategy for sustainable manufacturing. With Braincube, they rolled out their approach globally, enabling teams to improve yields, reduce downtime, and enhance quality.
Early wins led to remarkable results:
- 80% reduction in data preparation time, freeing teams to focus on innovation and problem-solving
- 100% autonomy for teams in building Product Clones, unlocking improved efficiency, higher yields, and confident decisions
- 165+ Product Clones built across 18 mills in under 3 years, accelerating their digital transformation at scale.
A sustainable culture of continuous improvement, aligned with long-term goals.
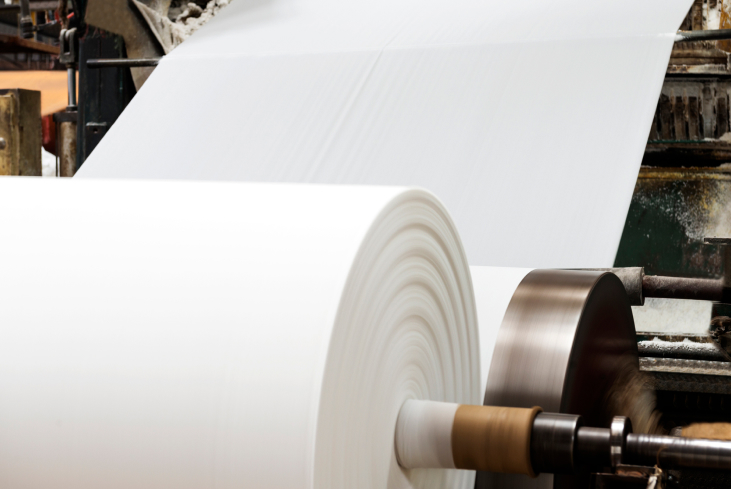
A Foundation for Future Success
Sappi’s journey with Braincube showcases the power of integrating data, people, and technology. By breaking silos and connecting teams with meaningful data, Sappi has set a new standard for digital transformation in the woodfibre industry.
“What we’ve built is more than a technical solution,” Boyd says. “It’s a culture of curiosity, collaboration, and confidence where every employee is empowered to innovate and excel.”
Through continuous improvement and alignment between corporate goals and plant-level execution, Sappi has redefined what’s possible in manufacturing, cementing their position as a leader in digital transformation.