Aligning Plant Performance with Corporate Ambitions
At Norske Skog Golbey—France’s largest newsprint paper factory—two production lines produced 600,000 tons annually, double the nation’s needs. Despite this impressive scale, frequent sheet breaks were a costly reality: seven per day halted production, costing $2,000 per break and nearly two hours of downtime daily.
For 20 years, the team tackled this issue with incremental fixes—adding chemicals, slowing speeds, tweaking equipment—but only addressed symptoms, not the root cause. The problem went beyond operations: operators were stressed, managers frustrated, and corporate goals increasingly out of reach.
“We had sensors across the production line measuring temperature, pressure, speed, and more, but no way to analyze how they interacted or pinpoint root causes,” recalls Fabrice Deladiennée, Golbey’s Industrial Director.
The plant director set a modest goal: reduce breaks by one or two per day. This improvement would save $1.2 million annually—helpful but not transformative.
At the time, the plant’s challenges seemed intractable, with corporate ambitions outpacing plant-level execution. That’s when Golbey turned to Braincube, embarking on a journey that would not only solve their problem but redefine their operations.
Understanding the Problem
For years, the Golbey team tackled the symptoms—adding chemicals to prevent stickies, slowing production speeds to minimize tension, investing in expensive new equipment—with little success. Operators fought fires daily, chasing incremental gains.
Braincube’s approach challenged the status quo: leveraged its proprietary Product Clones and CrossRank AI to analyze thousands of production variables.
The main culprit was the aging pulp, stored for over 36 hours before use. Contrary to popular wisdom, this practice was creating stickies—tiny adhesive clumps fueled by bacteria and bleaching agents. These stickies caused the catastrophic tears that disrupted production. The solution was counterintuitive and bold: switch to fresh pulp and overhaul established workflows.
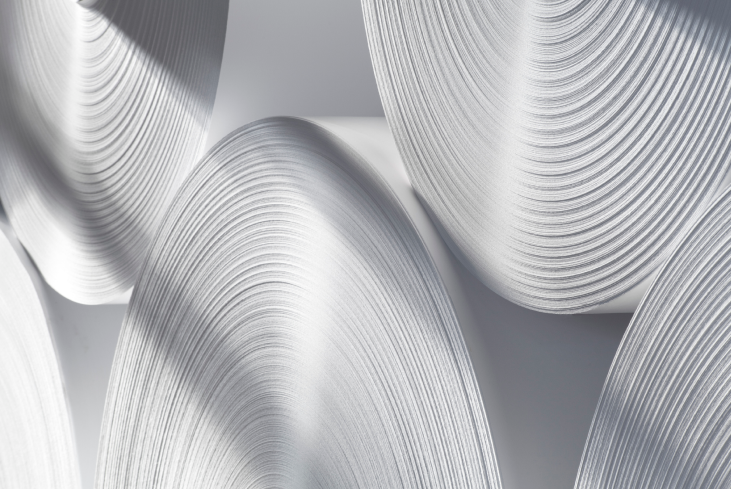
The Results: From Breaks to Breakthroughs
Convincing the team wasn’t easy. Initial resistance from the plant manager stemmed from fears of an insufficient pulp supply, which might add to daily downtime. But with a corporate champion supporting Braincube’s data-driven recommendations, the team made the leap.
The shift was implemented cautiously but decisively. And the results were immediate. The first day with fresh pulp brought no breaks. Then the second. Then the third. By the time two weeks had passed, Golbey had achieved what once seemed impossible: 14 consecutive days without a single tear.
The results spoke for themselves. Average daily breaks plummeted from seven to just 0.5. The immediate financial impact? A staggering $4 million saved in several months—more than triple the original $1.2 million annual target.
The Results: From Breaks to Breakthroughs
The transformation didn’t stop there. Freed from the constant disruptions, Golbey’s team increased production speeds by 12%, reduced chemicals, and slashed energy use.
The transformation wasn’t just operational – it was cultural. The plant moved from fire-fighting and scrabbling for incremental gains, to proactively uncovering hidden potential.
Braincube’s tools empowered Golbey to explore other opportunities for improvement. By systematically tackling challenges across the plant—from integrating more recycled paper to reducing emissions—they built a culture of continuous improvement.
Today, Braincube’s real-time analysis tools are embedded across Golbey’s operations, offering a unified view of production. Operators use intuitive dashboards to monitor parameters, receive deviation alerts and make proactive adjustments in real time. They are more empowered, less stressed.
Fresh Perspectives on Productivity
Norske Skog Golbey’s story isn’t just about fixing problems—it’s about redefining what’s possible. For decades, the plant was stuck in an optimization mindset, solving small problems while leaving massive potential untapped. With Braincube, they broke through these constraints to achieve extraordinary results, bridging the gap between corporate ambitions and plant-floor realities.
“What we’ve accomplished goes far beyond our initial expectations,” says Deladiennée. “Operators are still at the heart of the process, empowered by AI to work smarter and with less stress. This transformation is not just about technology; it’s about people, performance, and unlocking potential.”